Os métodos de revestimento do fotorresiste são geralmente divididos em revestimento por rotação, revestimento por imersão e revestimento por rolo, entre os quais o revestimento por rotação é o mais comumente usado. Por revestimento giratório, o fotorresistente é pingado no substrato, e o substrato pode ser girado em alta velocidade para obter um filme fotorresistente. Depois disso, um filme sólido pode ser obtido aquecendo-o em uma placa quente. O revestimento giratório é adequado para revestir desde filmes ultrafinos (cerca de 20 nm) até filmes espessos de cerca de 100um. Suas características são boa uniformidade, espessura de filme uniforme entre wafers, poucos defeitos, etc., podendo ser obtido um filme com alto desempenho de revestimento.
Processo de revestimento giratório
Durante o revestimento giratório, a velocidade de rotação principal do substrato determina a espessura do filme do fotorresistente. A relação entre a velocidade de rotação e a espessura do filme é a seguinte:
Rotação=kTn
Na fórmula, Spin é a velocidade de rotação; T é a espessura do filme; k e n são constantes.
Fatores que afetam o processo de revestimento por rotação
Embora a espessura do filme seja determinada pela velocidade de rotação principal, ela também está relacionada à temperatura ambiente, umidade, viscosidade do fotorresistente e tipo de fotorresistente. A comparação de diferentes tipos de curvas de revestimento fotorresistente é mostrada na Figura 1.
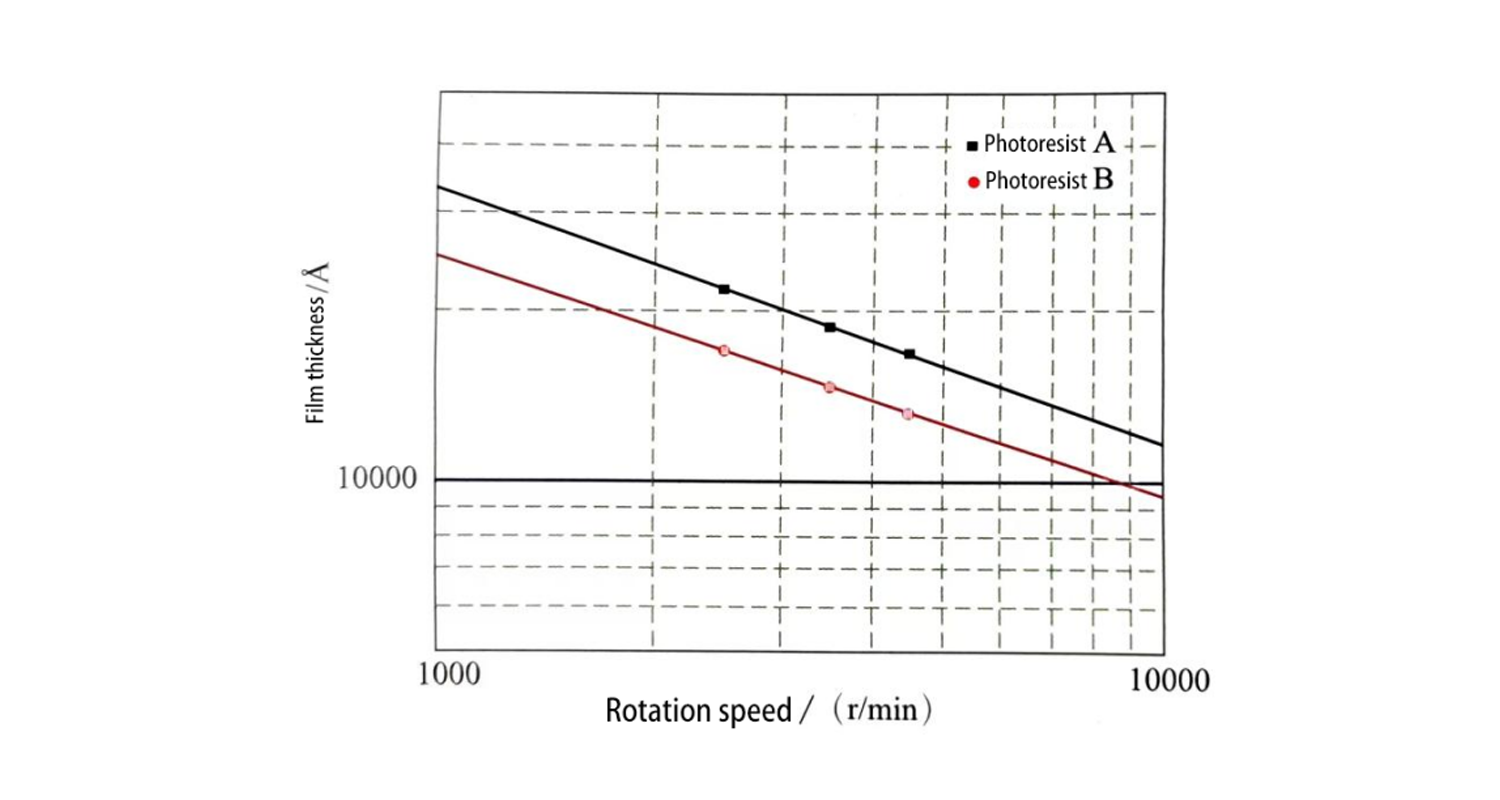
Figura 1: Comparação de diferentes tipos de curvas de revestimento fotorresistente
A influência do tempo de rotação principal
Quanto menor for o tempo de rotação principal, mais espessa será a espessura do filme. Quando o tempo de rotação principal aumenta, mais fino o filme se torna. Quando excede 20s, a espessura do filme permanece quase inalterada. Portanto, o tempo de rotação principal geralmente é selecionado para ser superior a 20 segundos. A relação entre o tempo de rotação principal e a espessura do filme é mostrada na Figura 2.
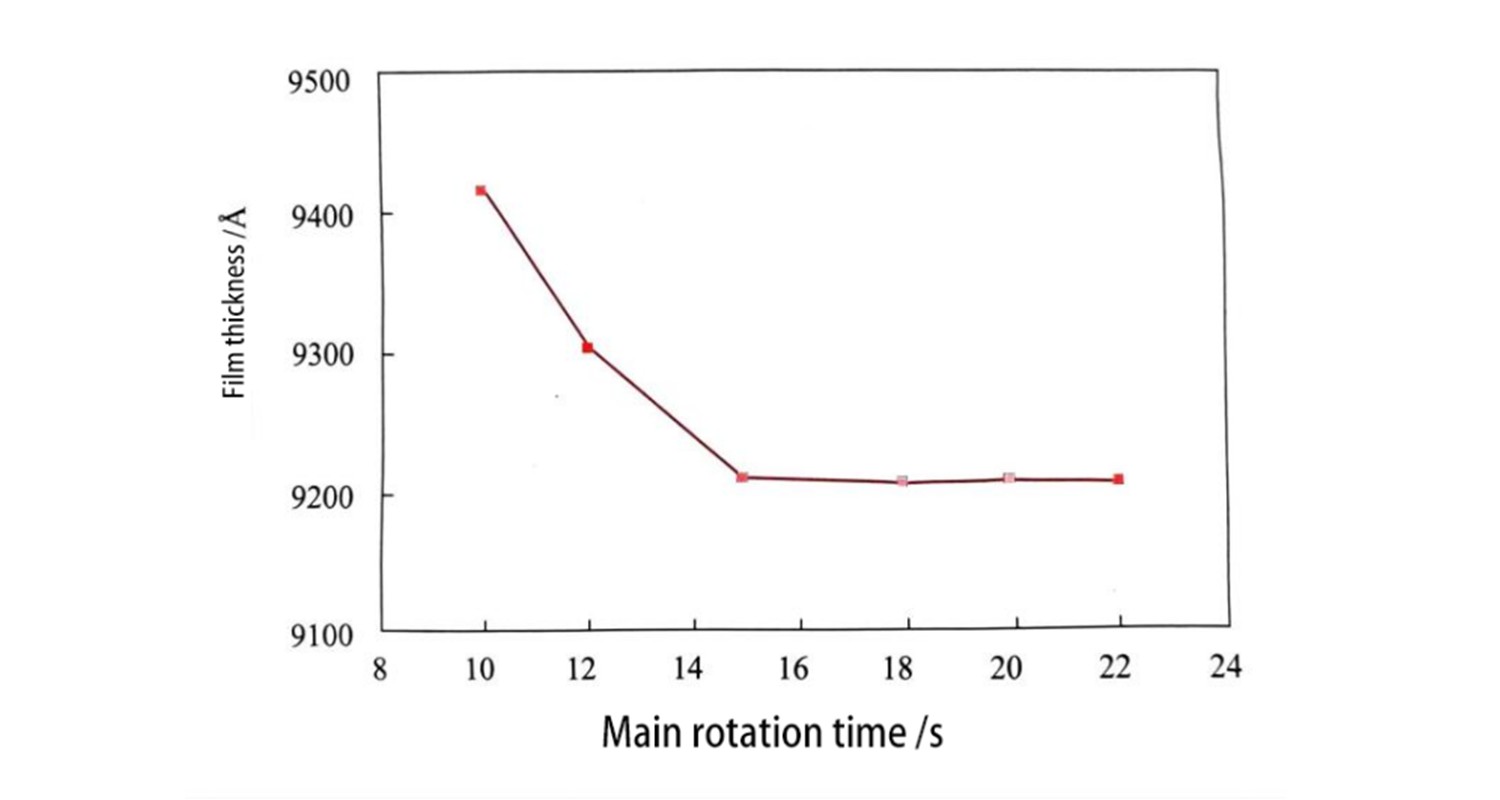
Figura 2: Relação entre tempo de rotação principal e espessura do filme
Quando o fotorresistente é gotejado no substrato, mesmo que a velocidade de rotação principal subsequente seja a mesma, a velocidade de rotação do substrato durante o gotejamento afetará a espessura final do filme. A espessura do filme fotorresistente aumenta com o aumento da velocidade de rotação do substrato durante o gotejamento, o que se deve à influência da evaporação do solvente quando o fotorresistente é desdobrado após o gotejamento. A Figura 3 mostra a relação entre a espessura do filme e a velocidade de rotação principal em diferentes velocidades de rotação do substrato durante o gotejamento do fotorresiste. Pode-se observar na figura que com o aumento da velocidade de rotação do substrato de gotejamento, a espessura do filme muda mais rapidamente, e a diferença é mais evidente na área com menor velocidade de rotação principal.
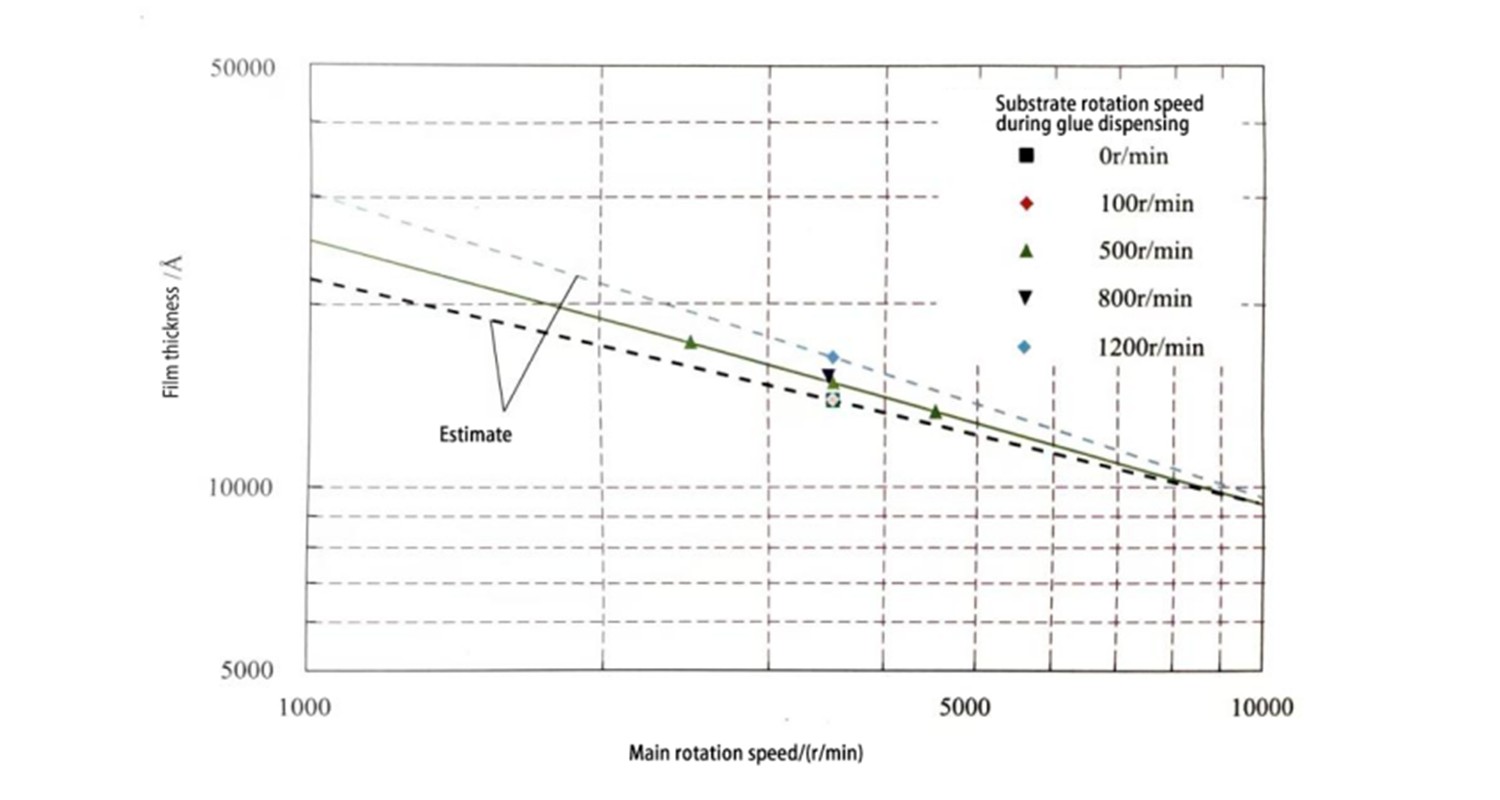
Figura 3: Relação entre a espessura do filme e a velocidade de rotação principal em diferentes velocidades de rotação do substrato durante a distribuição fotorresistente
Efeito da umidade durante o revestimento
Quando a umidade diminui, a espessura do filme aumenta, pois a diminuição da umidade promove a evaporação do solvente. No entanto, a distribuição da espessura do filme não muda significativamente. A Figura 4 mostra a relação entre a umidade e a distribuição da espessura do filme durante o revestimento.
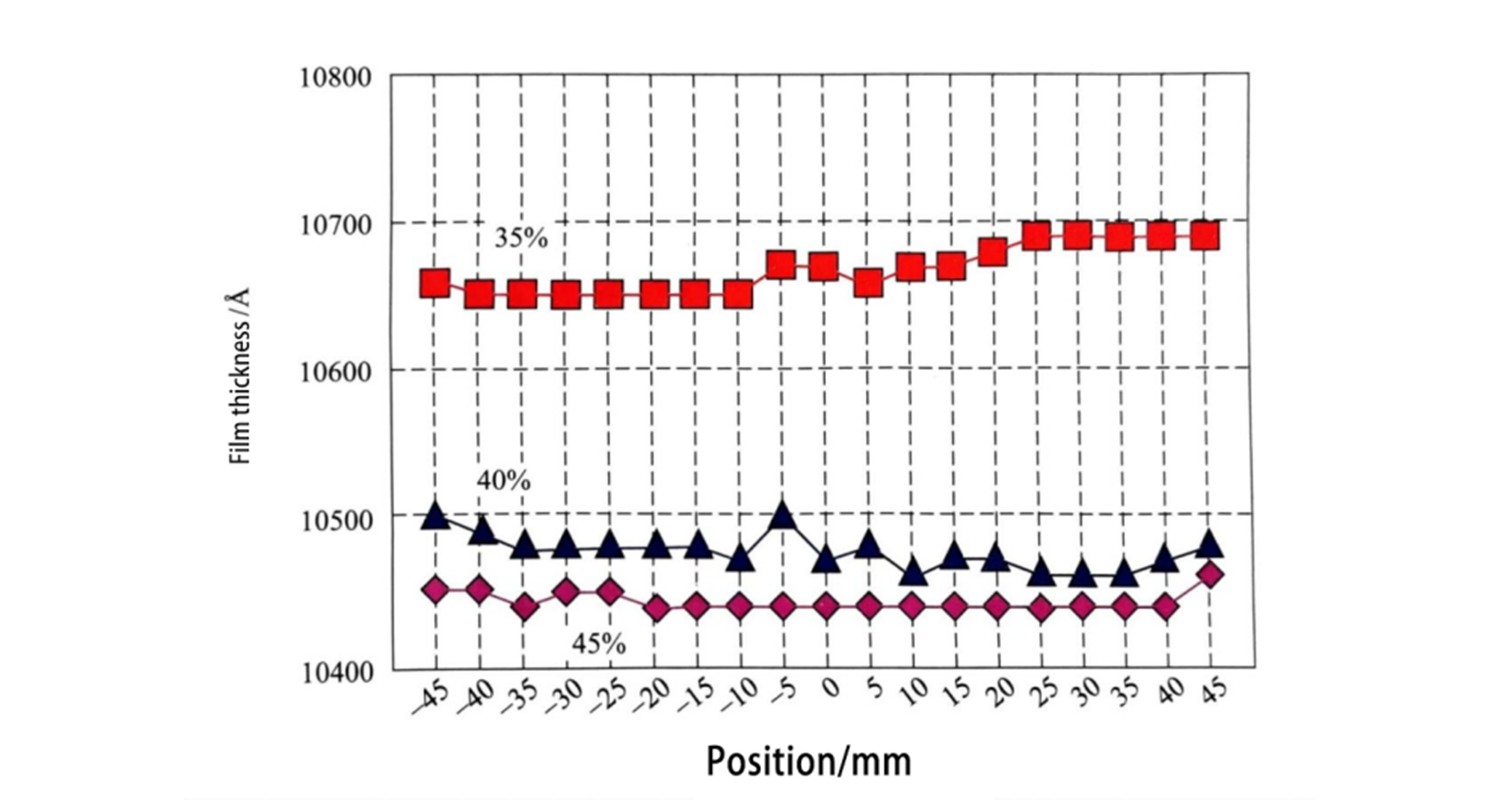
Figura 4: Relação entre umidade e distribuição da espessura do filme durante o revestimento
Efeito da temperatura durante o revestimento
Quando a temperatura interna aumenta, a espessura do filme aumenta. Pode-se observar na Figura 5 que a distribuição da espessura do filme fotorresistente muda de convexa para côncava. A curva na figura também mostra que a maior uniformidade é obtida quando a temperatura interna é de 26°C e a temperatura do fotorresiste é de 21°C.
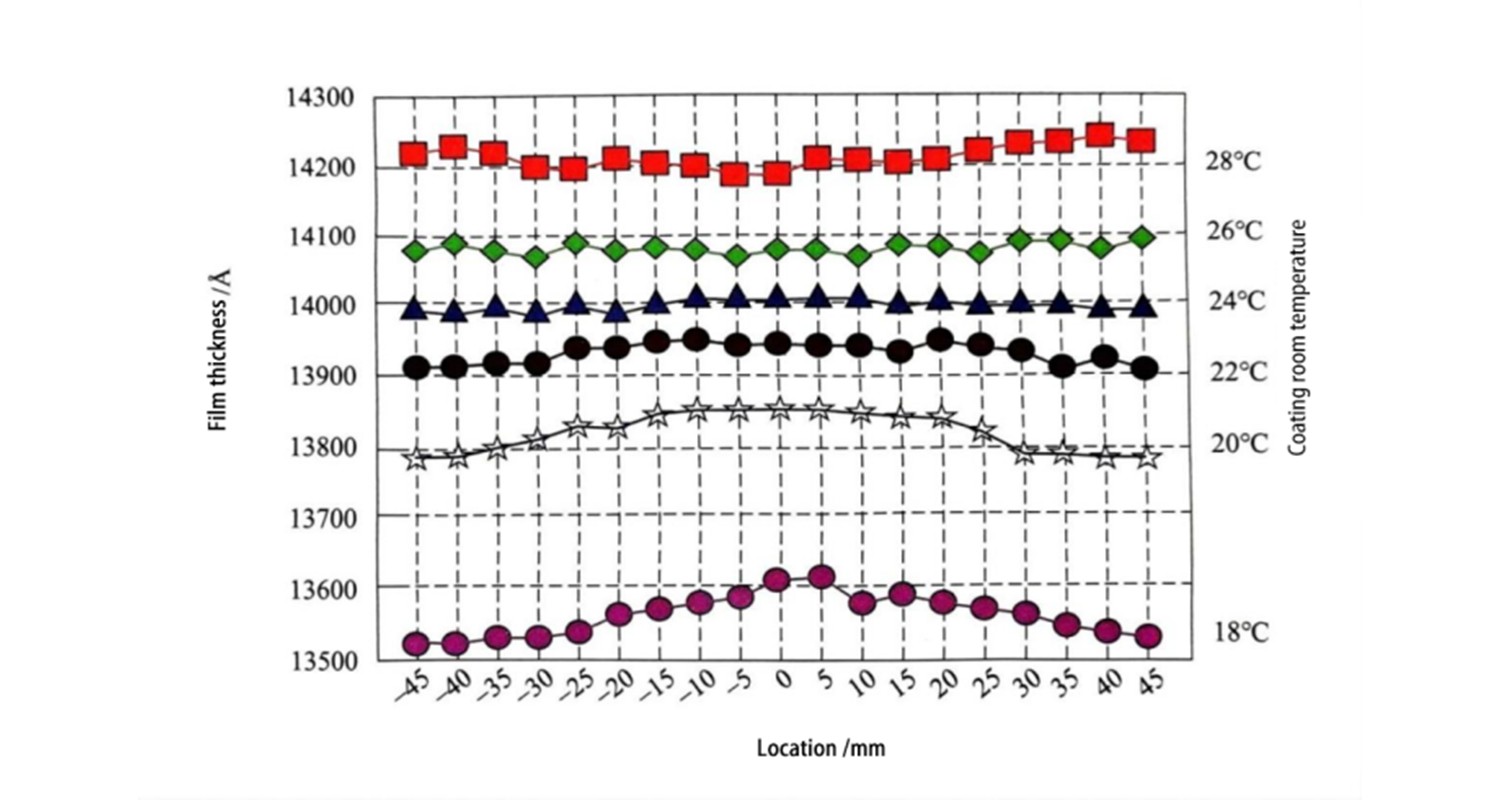
Figura 5: Relação entre temperatura e distribuição da espessura do filme durante o revestimento
Efeito da velocidade de exaustão durante o revestimento
A Figura 6 mostra a relação entre a velocidade de exaustão e a distribuição da espessura do filme. Na ausência de exaustão, mostra que o centro do wafer tende a engrossar. Aumentar a velocidade de exaustão melhorará a uniformidade, mas se aumentar demais, a uniformidade diminuirá. Pode-se observar que existe um valor ótimo para a velocidade de exaustão.
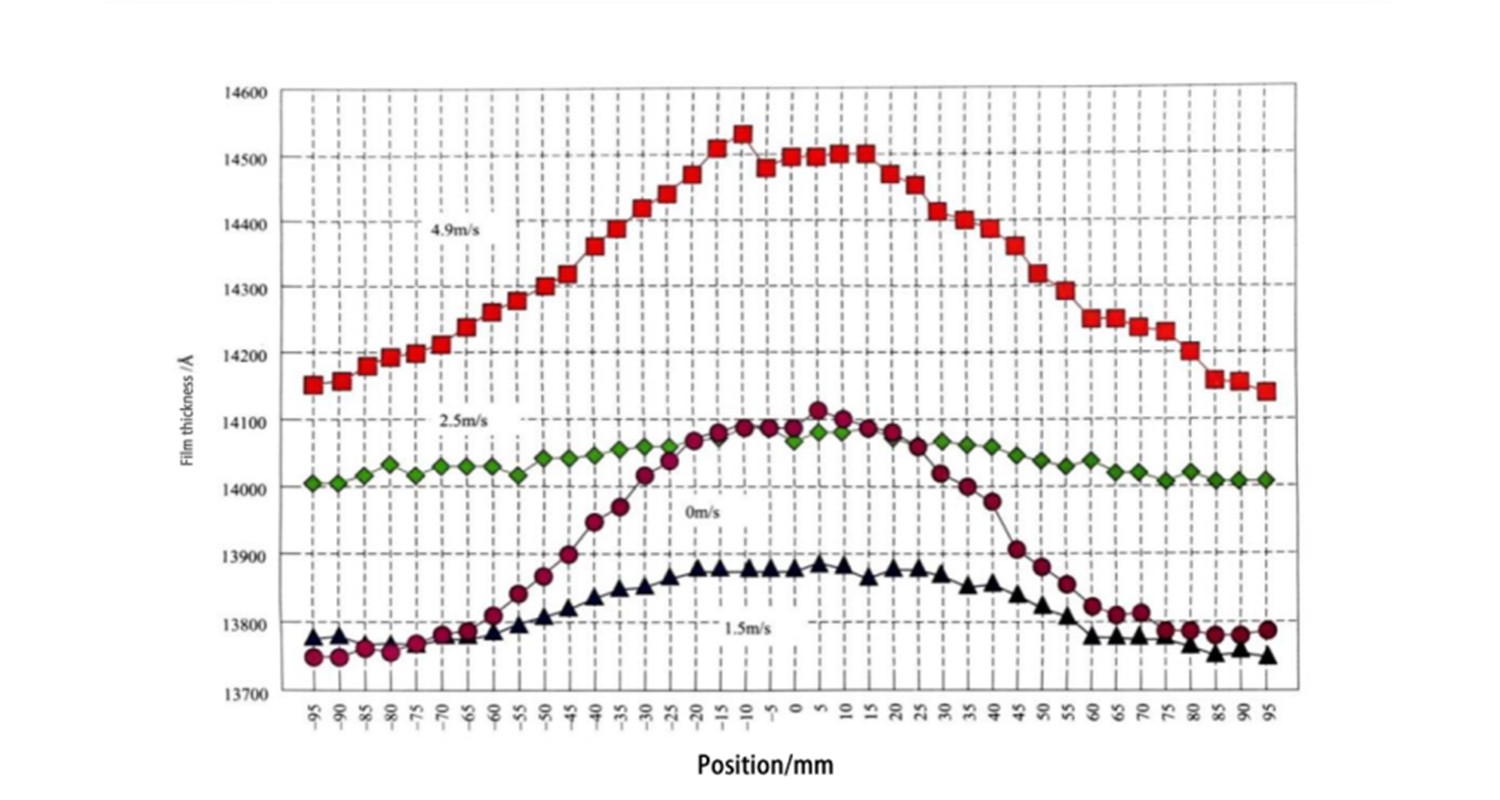
Figura 6: Relação entre velocidade de exaustão e distribuição da espessura do filme
Tratamento HMDS
Para tornar o fotorresistente mais revestível, o wafer precisa ser tratado com hexametildissilazano (HMDS). Especialmente quando a umidade se fixa à superfície do filme de óxido de Si, forma-se silanol, o que reduz a adesão do fotorresistente. Para remover a umidade e decompor o silanol, o wafer é geralmente aquecido a 100-120°C e a névoa HMDS é introduzida para causar uma reação química. O mecanismo de reação é mostrado na Figura 7. Através do tratamento HMDS, a superfície hidrofílica com um pequeno ângulo de contato torna-se uma superfície hidrofóbica com um grande ângulo de contato. O aquecimento do wafer pode obter maior adesão fotorresistente.
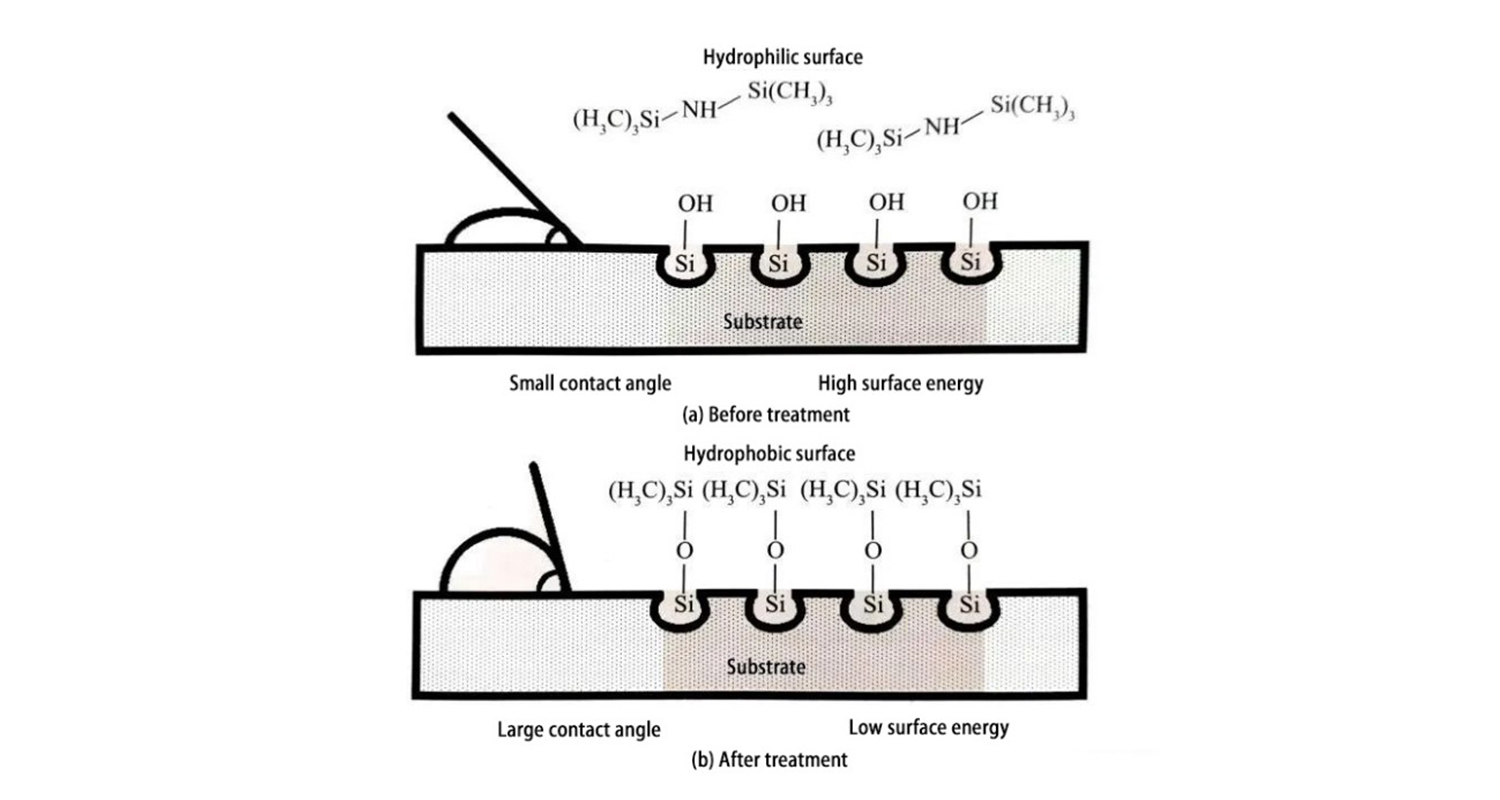
Figura 7: Mecanismo de reação HMDS
O efeito do tratamento HMDS pode ser observado medindo o ângulo de contato. A Figura 8 mostra a relação entre o tempo de tratamento HMDS e o ângulo de contato (temperatura de tratamento 110°C). O substrato é Si, o tempo de tratamento HMDS é superior a 1min, o ângulo de contato é superior a 80° e o efeito do tratamento é estável. A Figura 9 mostra a relação entre a temperatura de tratamento HMDS e o ângulo de contato (tempo de tratamento 60s). Quando a temperatura excede 120°C, o ângulo de contato diminui, indicando que o HMDS se decompõe devido ao calor. Portanto, o tratamento HMDS é geralmente realizado a 100-110°C.
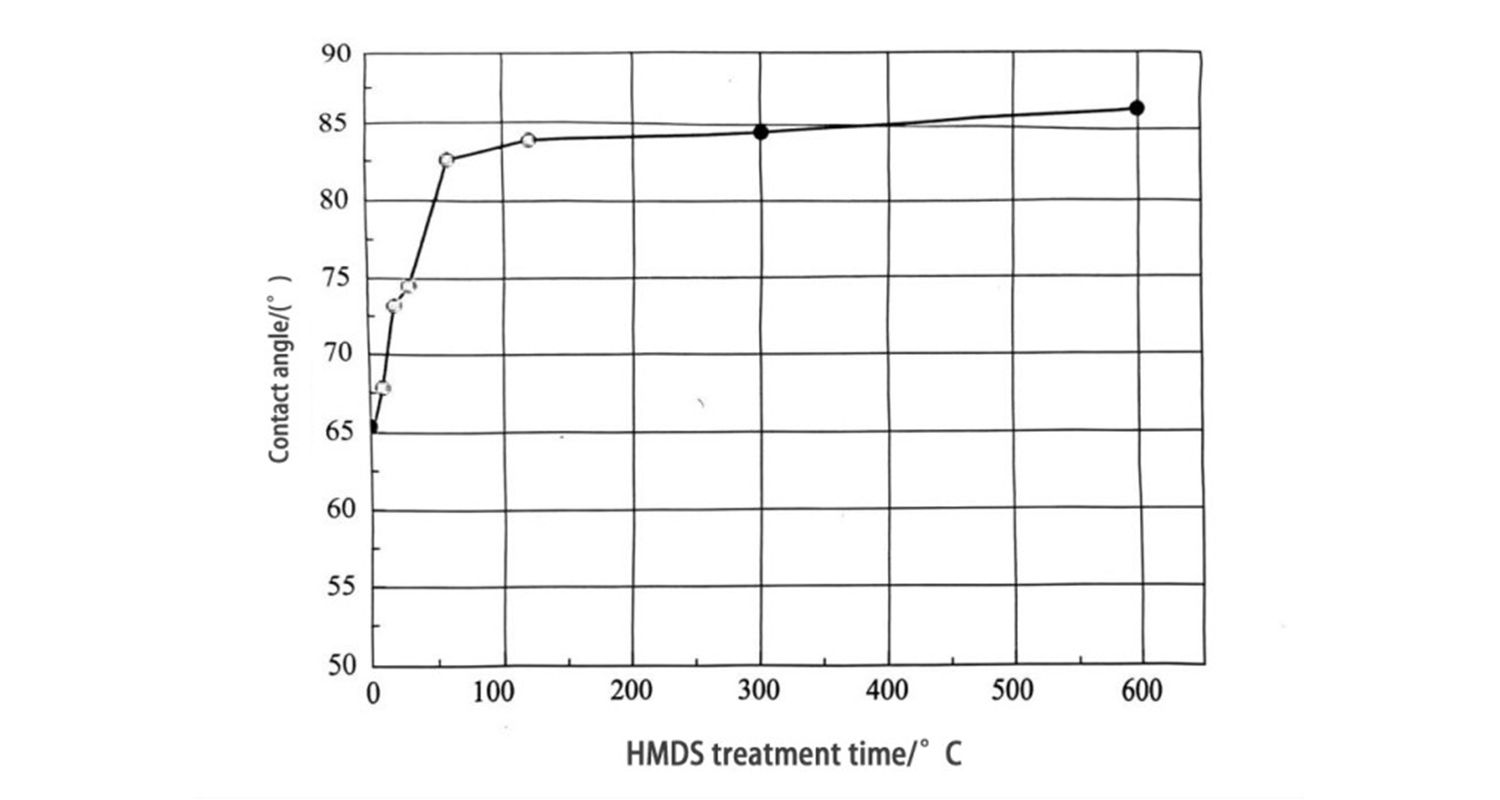
Figura 8: Relação entre o tempo de tratamento do HMDS
e ângulo de contato (temperatura de tratamento 110°C)
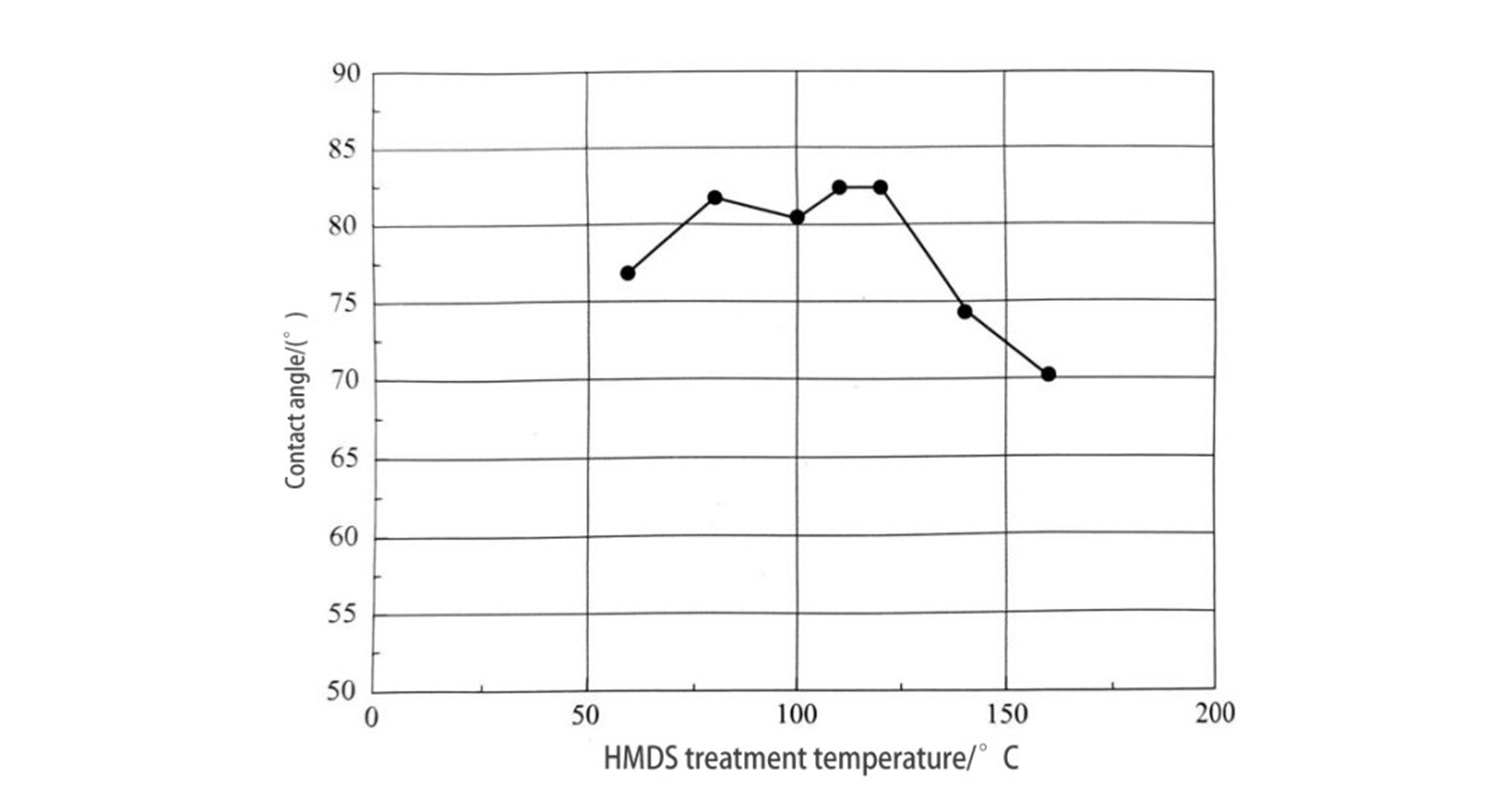
Figura 9: Relação entre temperatura de tratamento HMDS e ângulo de contato (tempo de tratamento 60s)
O tratamento HMDS é realizado em um substrato de silício com um filme de óxido para formar um padrão fotorresistente. O filme de óxido é então gravado com ácido fluorídrico com um tampão adicionado, e verifica-se que após o tratamento com HMDS, o padrão fotorresistente pode ser evitado. A Figura 10 mostra o efeito do tratamento HMDS (o tamanho do padrão é 1um).
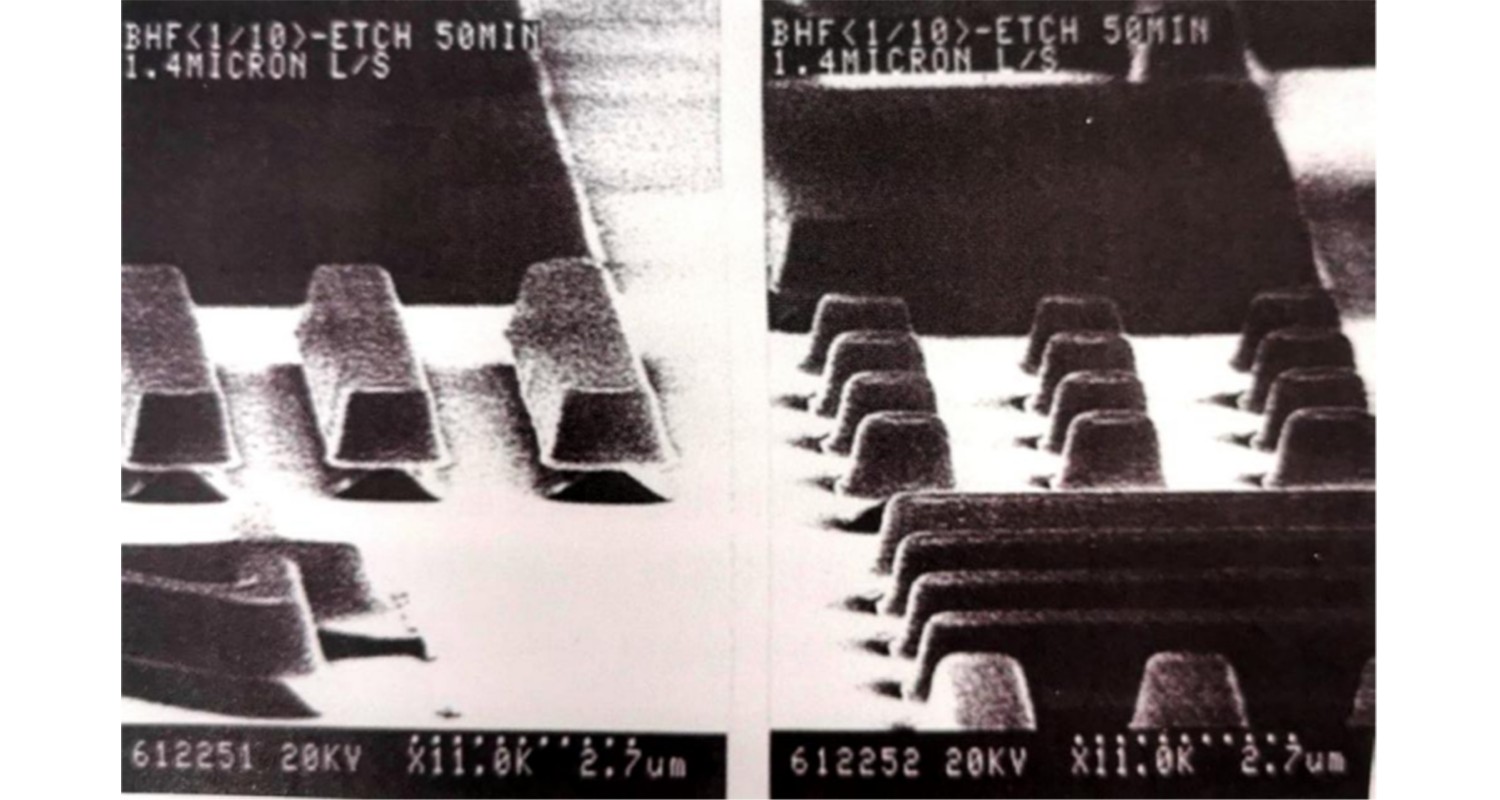
Figura 10: Efeito do tratamento HMDS (tamanho do padrão é 1um)
Pré-cozimento
Na mesma velocidade de rotação, quanto maior a temperatura de pré-cozimento, menor será a espessura do filme, o que indica que quanto maior a temperatura de pré-cozimento, mais o solvente evapora, resultando em uma espessura de filme mais fina. A Figura 11 mostra a relação entre a temperatura de pré-cozimento e o parâmetro A de Dill. O parâmetro A indica a concentração do agente fotossensível. Como pode ser visto na figura, quando a temperatura de pré-cozimento sobe acima de 140°C, o parâmetro A diminui, indicando que o agente fotossensível se decompõe a uma temperatura superior a esta. A Figura 12 mostra a transmitância espectral em diferentes temperaturas de pré-cozimento. A 160°C e 180°C, um aumento na transmitância pode ser observado na faixa de comprimento de onda de 300-500nm. Isto confirma que o agente fotossensível é cozido e decomposto a altas temperaturas. A temperatura de pré-cozimento tem um valor ideal, que é determinado pelas características e sensibilidade da luz.
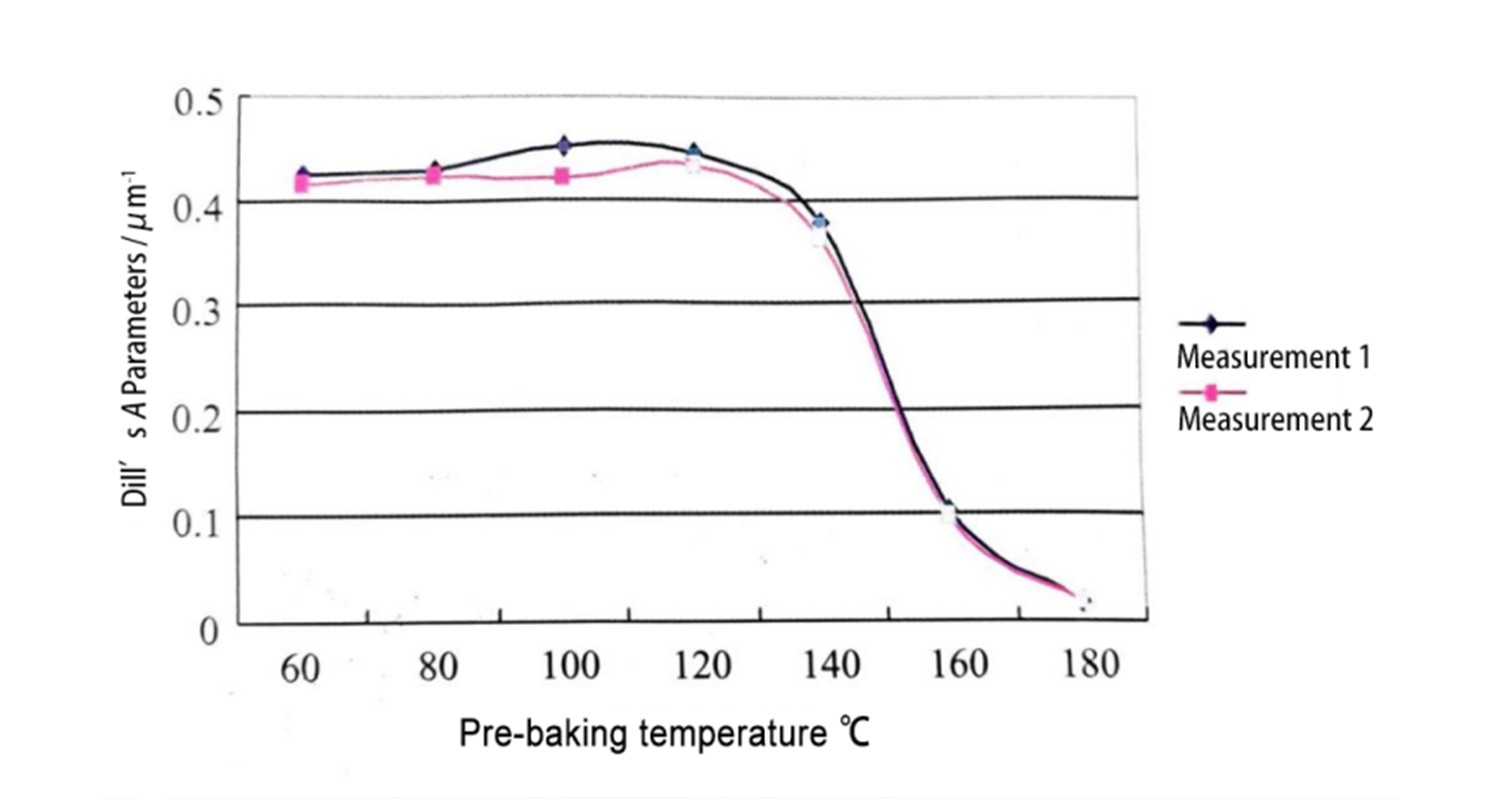
Figura 11: Relação entre a temperatura de pré-cozimento e o parâmetro A de Dill
(valor medido de OFPR-800/2)
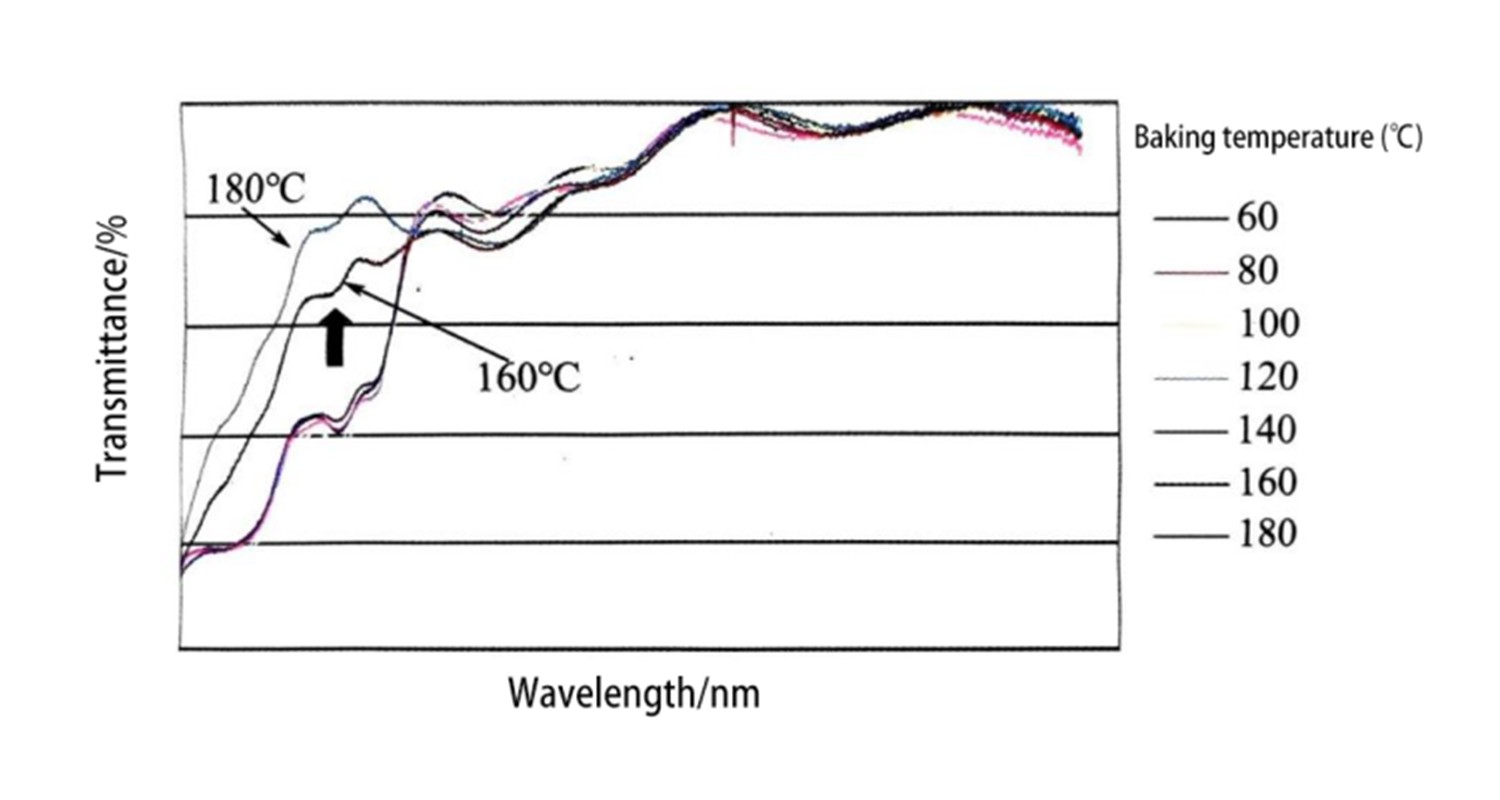
Figura 12: Transmitância espectral em diferentes temperaturas de pré-cozimento
(OFPR-800, espessura de filme de 1um)
Em suma, o método de revestimento giratório tem vantagens únicas, como controle preciso da espessura do filme, desempenho de alto custo, condições de processo suaves e operação simples, por isso tem efeitos significativos na redução da poluição, economia de energia e melhoria do desempenho de custos. Nos últimos anos, o revestimento por rotação tem ganhado cada vez mais atenção e sua aplicação gradualmente se espalhou por vários campos.
Horário da postagem: 27 de novembro de 2024